Table of Contents
3D printing, also known as additive manufacturing, has emerged as a transformative technology with significant implications for manufacturing and design. By creating three-dimensional objects layer by layer from digital models, 3D printing offers unprecedented levels of customization, efficiency, and innovation. This article explores how 3D printing is reshaping the manufacturing industry, revolutionizing design processes, and presenting both opportunities and challenges.
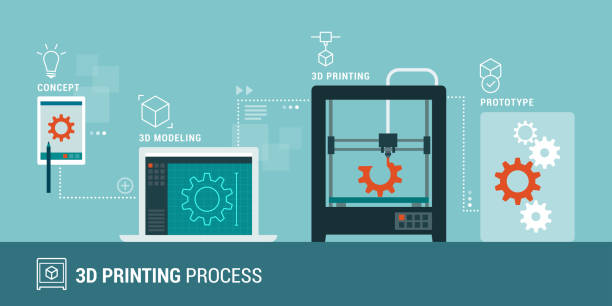
The Fundamentals of 3D Printing
1. What is 3D Printing?
3D printing is a process of creating three-dimensional objects from a digital file. It involves adding material layer by layer until the final product is formed. Various technologies and materials are used in 3D printing, including:
- Fused Deposition Modeling (FDM): A common method that extrudes melted thermoplastic material through a nozzle to build objects layer by layer.
- Stereolithography (SLA): Uses ultraviolet light to cure liquid resin into solid layers.
- Selective Laser Sintering (SLS): Employs a laser to fuse powdered material into solid objects.
2. Materials Used in 3D Printing
3D printing can use a variety of materials, including:
- Plastics: Such as PLA, ABS, and PETG, commonly used for prototypes and consumer products.
- Metals: Including stainless steel, titanium, and aluminum, used for industrial applications and aerospace components.
- Resins: Specialized resins for high-resolution and detailed prints.
- Composites: Materials combined with fibers or particles to enhance properties like strength and durability.
Impact on Manufacturing
1. Customization and Personalization
3D printing allows for high levels of customization, enabling manufacturers to produce bespoke products tailored to individual needs.
- Customized Products: Consumers can order customized items such as personalized jewelry, custom prosthetics, or unique home décor.
- On-Demand Production: Companies can produce small batches of customized products without the need for large-scale manufacturing runs.
2. Rapid Prototyping
One of the most significant advantages of 3D printing is its ability to rapidly produce prototypes and iterate designs.
- Faster Development: Designers and engineers can quickly create and test prototypes, accelerating the product development cycle.
- Cost-Effective: 3D printing reduces the cost and time associated with traditional prototyping methods, such as injection molding or machining.
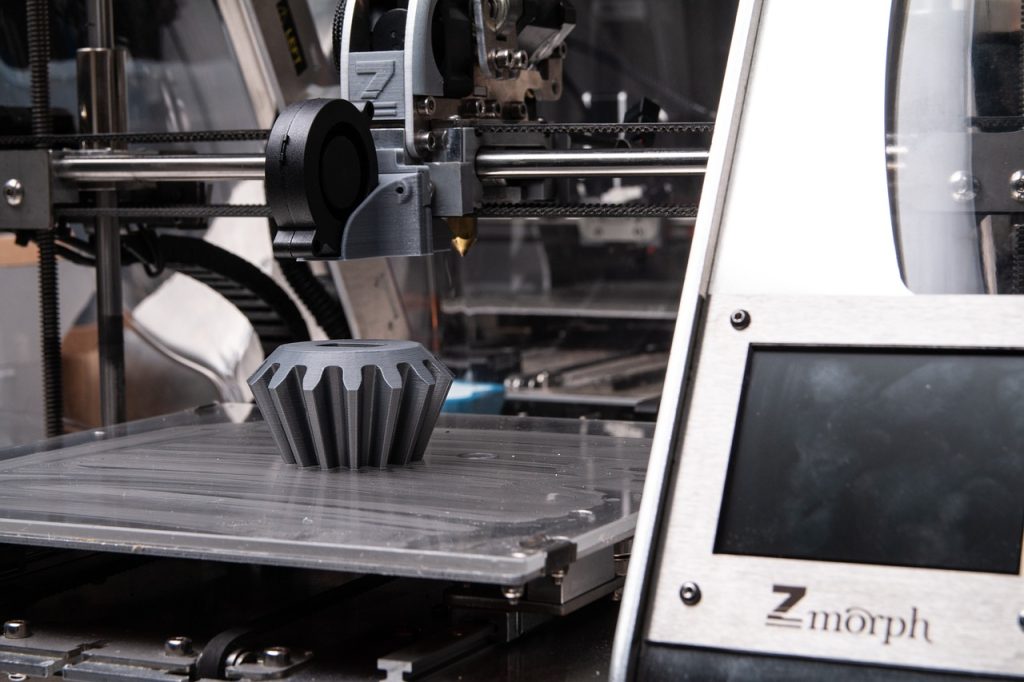
3. Reducing Waste
Traditional manufacturing processes often generate significant waste through subtractive methods, where material is cut away to create a product. In contrast, 3D printing is additive, building objects layer by layer and minimizing waste.
- Material Efficiency: Only the material needed to build the object is used, reducing waste and conserving resources.
- Sustainable Practices: Many 3D printing materials are recyclable or biodegradable, contributing to more sustainable manufacturing practices.
4. Supply Chain Disruption
3D printing can disrupt traditional supply chains by enabling localized production and reducing reliance on complex logistics.
- Localized Manufacturing: Products can be produced on-site or close to the point of use, reducing transportation costs and lead times.
- On-Demand Production: The ability to produce parts as needed can eliminate the need for large inventories and reduce storage costs.
Impact on Design
1. Design Freedom and Complexity
3D printing offers designers greater freedom to create complex and intricate shapes that would be difficult or impossible to achieve with traditional manufacturing methods.
- Complex Geometries: Designers can create structures with intricate details, internal cavities, and organic shapes that are not feasible with conventional techniques.
- Innovative Designs: The ability to experiment with new forms and structures encourages creativity and innovation in design.
2. Iterative Design Process
3D printing facilitates an iterative design process, allowing designers to make modifications and improvements quickly.
- Rapid Testing: Designers can quickly produce and test multiple iterations of a design, leading to better and more refined products.
- Feedback Integration: Rapid prototyping allows for immediate feedback and adjustments based on user input or testing results.
3. Collaboration and Accessibility
3D printing technology promotes collaboration and accessibility in design and manufacturing.
- Collaborative Design: Designers, engineers, and manufacturers can work together more effectively by sharing digital files and prototypes.
- Accessible Technology: The availability of affordable 3D printers and user-friendly design software has democratized access to manufacturing and design capabilities.
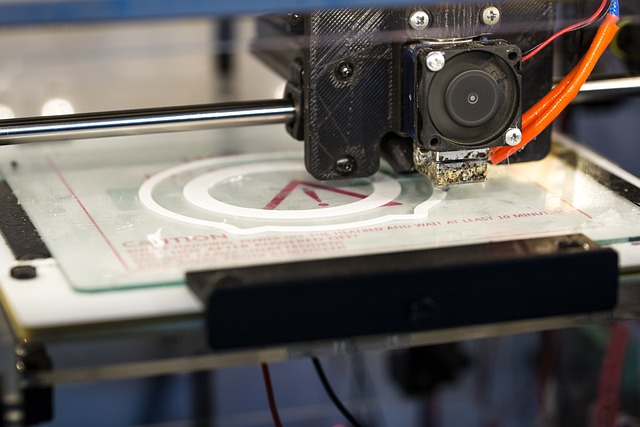
Challenges and Considerations
1. Material Limitations
While 3D printing offers a wide range of materials, some applications require properties that current 3D printing materials cannot yet provide.
- Material Strength: Some 3D printing materials may not match the strength or durability of traditional manufacturing materials, limiting their use in certain applications.
- Material Costs: High-quality or specialized materials can be expensive, impacting the cost-effectiveness of 3D printing for some applications.
2. Intellectual Property Concerns
The digital nature of 3D printing raises concerns about intellectual property (IP) protection and the potential for unauthorized copying of designs.
- Design Theft: The ease of digital distribution and replication of 3D models poses risks of design theft and IP infringement.
- Protection Measures: Designers and manufacturers need to implement strategies to protect their IP, such as digital rights management or secure file sharing systems.
3. Quality Control and Standards
Ensuring consistent quality and adherence to industry standards can be challenging with 3D printing, particularly as the technology evolves.
- Quality Assurance: Implementing quality control measures and adhering to standards is essential to ensure the reliability and performance of 3D-printed products.
- Regulatory Compliance: Compliance with industry regulations and standards is necessary, particularly for applications in sectors like healthcare or aerospace.
Conclusion
3D printing is transforming manufacturing and design by offering unprecedented customization, rapid prototyping, material efficiency, and design freedom. Its impact extends across various industries, from consumer products and healthcare to aerospace and architecture. While challenges such as material limitations, intellectual property concerns, and quality control remain, the potential benefits of 3D printing continue to drive innovation and reshape traditional manufacturing and design processes. As technology advances and becomes more integrated into everyday applications, 3D printing is poised to play a central role in the future of production and creativity.